BMP Medical: Plastic Injection Molding Process Guide
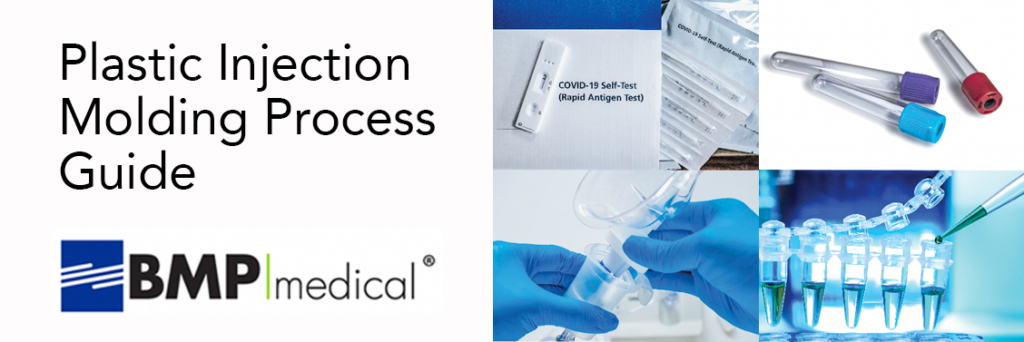
In this blog titled “Plastic Injection Molding Process Guide”, produced by the subject matter experts at BMP Medical, we offer educational information that will help you build better injection molded medical devices and components.
What is plastic injection molding?
Simply stated, the plastic injection molding process injects heated plastic substrates into a metal-tooled cavity of the desired shape and it is allowed to dry, cure, and set.
But not so quick—let’s do a deeper dive into the step-by-step processes and the caveats evolved throughout the entire process to manufacture a finished plastic injection-molded medical device.
The plastic injection molding manufacturing process is ideal for consistently producing finished components or parts in a cost-effective manner. The up-front tooling process can be rather costly, so it is really only suitable for medium- to large-volume manufactured parts. This manufacturing process produces very little material waste, and the leftover thermoplastics can be recycled.
SIM
Scientific injection molding (SIM) is a data-driven, scientific approach. Cycle times are minimized, machine efficiencies are improved, and productivity is increased. Scientific injection molding is a strong tool supporting the objectives and practices of a lean manufacturing culture. SIM reduces or eliminates many of the forms of waste by providing a robust, predictable molding process.
Plastic injection molding guide process:
First, based on your CAD drawings and 3D printed prototype, a decision needs to be made on which injection molding process is best.
Commonly used plastic manufacturing techniques
The most commonly used plastic manufacturing techniques are injection molding, injection blow molding, two-shot molding, insert molding, rotational molding, compression molding, extrusion molding, and thermoforming. The requirements and specifications of your finished product will determine which injection molding process is best for your finished part.
What is plastic injection molding?
Injection molding is ideal for many small precision medical and large automotive part applications. This is the most commonly used plastic manufacturing process, and it offers a great deal of flexibility in material choices that can change the appearance of the final product.
What is plastic injection blow molding?
Injection blow molding is used in manufacturing parts that need to be hollow and maintain a uniform wall thickness. This process utilizes the blowing of air into the thermoplastic cavities until the desired shape is formed. Bottles are a common product manufactured by this method.
What is plastic two-shot molding?
Two-shot molding has a few names, it is also known as 2-shot, dual-shot, and double-shot molding. This process combines two parts into a single molded part by combining two machining processes. It offers flexibility for combining different resins materials together.
What is plastic insert molding?
This is a single-step process where two parts are formed together. This process is best suited for parts that need to form together tightly.
Plastic injection molding guide considerations:
Key considerations for the manufacturing process selection and thermoplastics material choice:
• Overall design
• Functionality
• Shelf life of the product
• Cost
• Tensile strength
• Shock absorbance
• Impact tolerance
• Scratch resistance
• Heat resistance
• Performance
• Stability
• Chemical resistance
• Final product weight
• UV protection
Plastic injection molding guide Thermoplastic Material Selection
Which medical-grade thermoplastic should be used for manufacturing the medical product?
• Polyethylene
• Polypropylene
• Polystyrene
• Polymethyl methacrylate
• Polyvinyl chloride
• Polyamides (nylons)
• Acrylonitrile butadiene styrene (ABS)
• Polycarbonate
Our blog Common Thermoplastics in Injection Molding provides an in-depth review of the different thermoplastics used in medical products, their key benefits, and their tensile strength in psi. Given the precision required in most medical devices, it is generally best to avoid resins that have asymmetrical shrinkage.
Injection Molding Tooling
Mold tooling is essential in producing an accurate and cost-effective manufactured product.
These key tool-making considerations need to be made before the injection molding process can begin:
• Cooling compensation
• Tool mold size and material selection
• Designing, building, and debugging the mold
• Gate placement
• Polishing process, mold fitting, and assembly
• Mold fitting and trial prototyping
How the injection molding press works
The Injection molding manufacturing process
Injection molding is a very complex process. The actual machine has three major parts: the injection unit, the mold section, and the clamp. Thermoplastic pellets are fed into the hopper of the unit and then pushed into the barrel. A turning screw pushes the thermoplastic pellets forward. Heater bands surround the injection unit, melting the thermoplastic pellets. The screw continues to turn, pushing the molten into the open cavity area of the mold. It opens and the part is ejected. The mold closes and the process repeats.
Injection molding monitoring is an ongoing process
The machine operator and engineer continuously monitor the following predetermined parameters to deliver a quality product:
• Injection plasticizing pressure
• Mold, nozzle, air, melt, and cooling temperature
• Filling time
• Packaging and holding time
Why BMP Medical should be your next plastics manufacturing partner
Located in the United States, BMP Medical is near Leominster, Massachusetts, where Pioneer Plastic City was founded, and the region has many thriving plastic manufacturing companies.
BMP Medical provides plastic contract manufacturing services to leading medical device and diagnostic OEMs in need of injection molding, injection blow, two-shot, and insert molding. BMP Medical’s 80,000 sq. ft. facility is located in Sterling, Massachusetts. We foster strong trust-driven relationships to develop inventive solutions tailored to customer and end-user needs.
From concept through commercialization, BMP offers in-depth problem-solving backed by deep industry knowledge and operational excellence.
BMP Medical is a global contract manufacturer servicing the Medical Device and Medical Diagnostic markets in all areas, including, but not limited to, IVD, IV access, sample-preparation devices, and lateral-flow technologies. Headquartered in Sterling, Massachusetts, BMP Medical can service our partner requirements on a worldwide basis.
Certifications: ISO13485:2016; FDA registration #1220502; ISO Class 8 injection molding; ISO Class 8 assembly & packaging; 21 CFR 820 Quality System Regulation; FDA registered; MedAccred Certified
Services Offered:
• Class 7 Assembly
• Clean Room Manufacturing (Class 8)
• Clean Room Packaging and Assembly (Class8)
• Custom Two-shot Molding
• Custom Assembly & Packaging
• Custom Injection Blow Molding (IBM)
• Custom Injection Molding
• Custom Insert Molding
• DNase- and RNase-free manufacturing
• FDA Registered Facility
• Pad printing
• Product design & development services
• R&D tooling
• Sterilization services
Get to know BMP Medical today: https://bmpmedical.com/
BMP Medical, a Chamfr Service Partner, is a plastic manufacturing hub for your custom components & finished devices. Check out our Service Partner page for more partners to help you execute on your design & development project.
Let’s keep in touch.
Don’t miss seller news, product alerts, and insights. Sign up for our emails to receive updates directly in your inbox.